MTI Journal
MTI Journal.11
Measuring the Propeller Working Conditions in Actual Sea
Norihide Igarashi
Researcher, Maritime and Logistics Technology Group*
*The job title is as of February 25, 2020
Since February 2018, I have been seconded to MTI and am mainly engaged in R&D activities related to the propulsion performance of ships. Although the NYK Group is addressing the reduction of environmental loads of ships from both the hardware and software sides, improving propulsion performance (improving fuel efficiency) should contribute to reducing environmental loads from the hardware side. So far, shipyards and shipping companies have striven for realizing high-performance ships, but for realizing more reduction of environmental loads, further improvement and upgrading are expected. In this article, I would like to introduce R&D on propellers (screw propellers), which affect the propulsion performance of ships greatly.
Aiming for Further Improvement of Propellers
Propellers are important parts for propelling ships. Depending on the propeller performance, ship performance will greatly change. Therefore, for building more high-performance and energy-efficient ships, we need more improved propellers, which are designed by shipyards or propeller manufacturers. For designing, they check the propeller performance by considering ship type, the expected ship speed, and the main engine speeds of target ships, and derive an optimal propeller shape by using towing tank tests or CFD (computational fluid dynamics). As high-performance ships are expected these days, designers are striving to improve propellers by even one percent day to day.
Challenge for “Actual Sea”
The big problem in designing propellers is that we cannot grasp the propeller movements in actual sea, which means we cannot thoroughly grasp how well propellers are working underwater. If propellers are working under a condition completely different from the initial calculation at the design stage, they cannot work as well as expected. Consequently, the whole ship performance possibly cannot reach the initial expectation.
Why can’t towing tank tests and CFD simulate the actual sea conditions? That problem is related to the size of objects. First, when we conduct a towing tank test, obviously actual ships and propellers cannot be used, for they are too big. Therefore, we use scaled-down models for the test. But the size difference between a model and an actual ship affects the flow field – the water flow near the ship and the propeller. So, the flow field of a model and that of an actual ship differ, which difference is called the “scale effect.” When the estimated accuracy of scale effect is low, propellers might not be able to demonstrate the expected power to propel the ship.
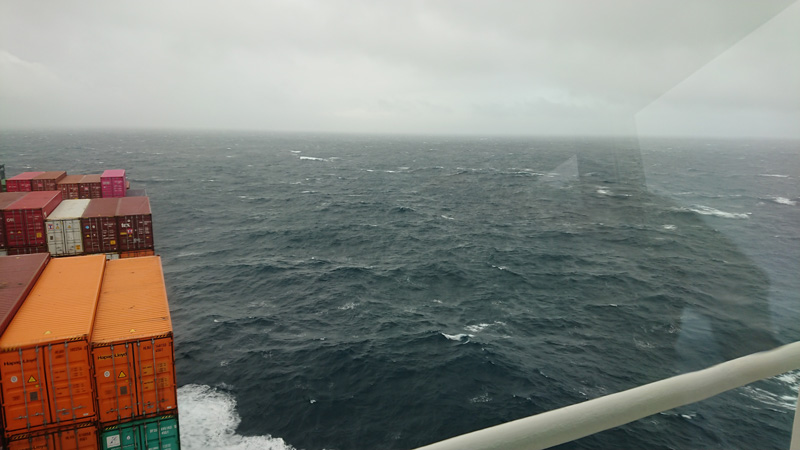
An ocean-going ship in the actual sea, a world that cannot be anticipated only by calculation
As for CFD, it is possible for recent computers to calculate for both a model and an actual ship, which is subject to the scale effect. So, you might think that we can calculate for an actual ship size using CFD, but it is not quite true, because it is very difficult to confirm on an actual ship if the CFD result is correct or not. Here is the point in challenging for the actual sea. If we can get measured data of propellers in the actual sea, the data should be set as the correct answer, and so we can verify the accuracy of the CFD calculated result for the actual ship scale. If we can get CFD that can duplicate the actual sea conditions accurately, based on the calculation, we can design propellers that are optimized for the actual sea. Consequently, more high-performance propellers and high-performance ships can be realized.
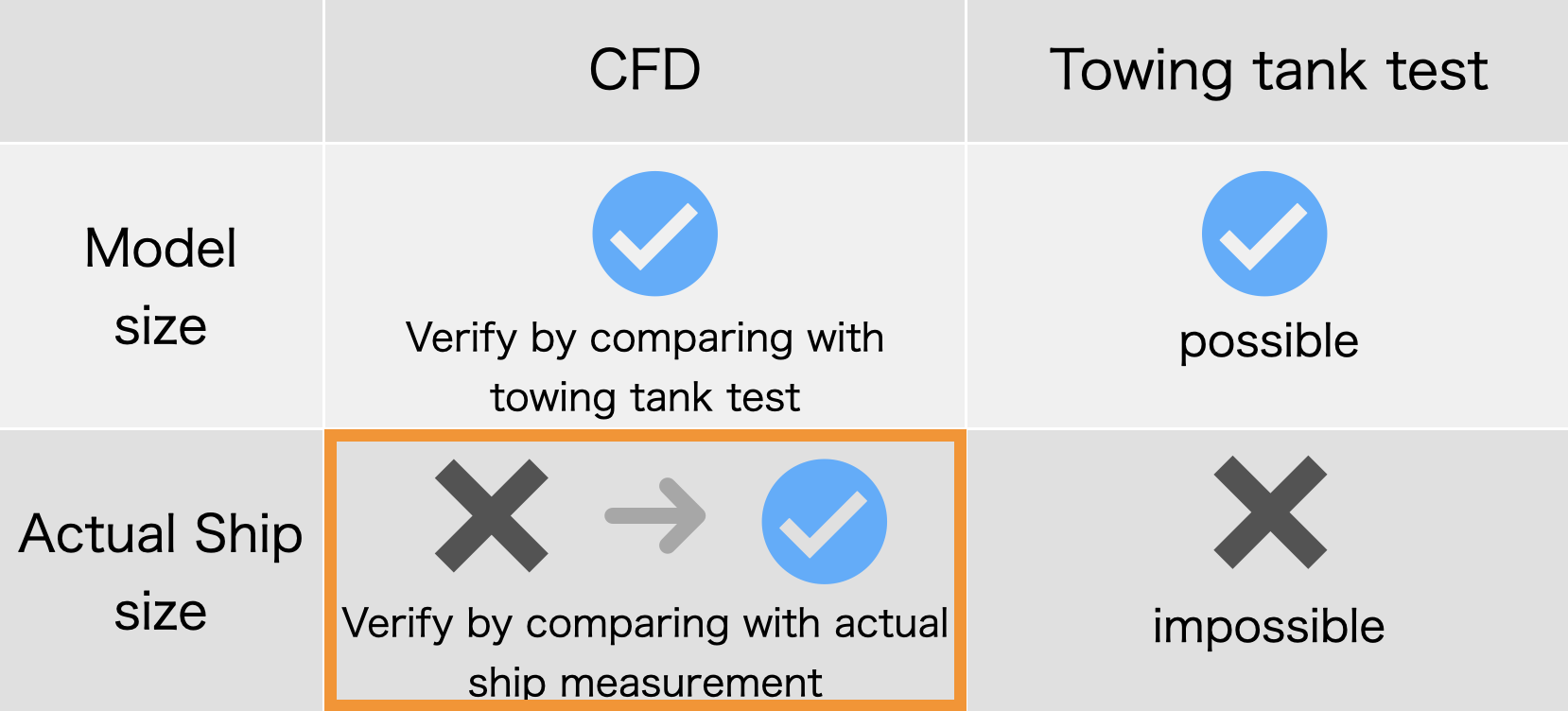
This time, we were able to verify the CFD for the actual ship scale (in the orange frame)
Establishing the Structure of the Joint R&D for Measuring in the Actual Sea
It is impossible for a shipping company alone to measure and analyze actual-sea conditions. The knowledge of shipyards, which design ships and propellers, is essential for considering optimal measuring points and reflecting measured results to designing. Further, without the cooperation of the measuring-device manufacturer, we cannot adjust the device and analyze the data.
So, NYK and MTI started a joint research project with JMU, Japan Marine United Corporation, and Furuno, Furuno Electric Co., Ltd., for measuring the propeller operating conditions in actual sea, targeting 14,000 TEU containerships.
Under this joint research, each company cooperated toward the same target. JMU decided the layout of equipment and installed the equipment to a newbuilding. NYK and MTI coordinated the whole project planning and development and installation of the measuring equipment, and also proceeded the measurement without any trouble while coordinating with the actual site for preventing any ship delay and confirmed whether all the required conditions for the measurement were met.
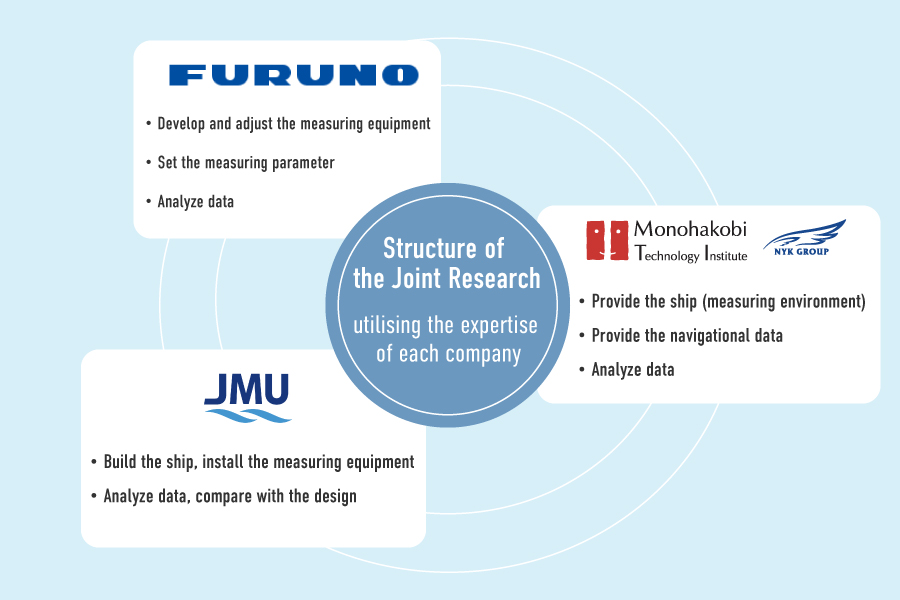
On-Board Measurement, Collection of Actual-Sea Data
After the ship was delivered, engineers from each company embarked on it and measured the conditions of propeller movement in actual sea. Measurement here mainly refers to measurement of the stern flow field, observation of the propeller cavitation, and measurement of fluctuating pressure on the stern.
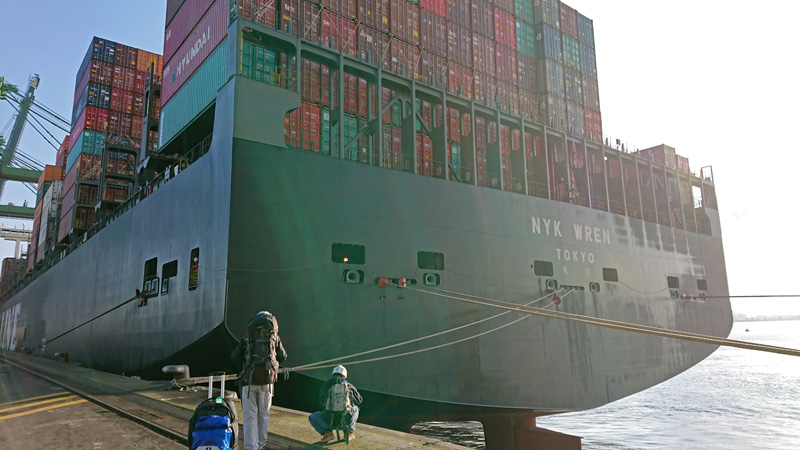
Just before the embarkation
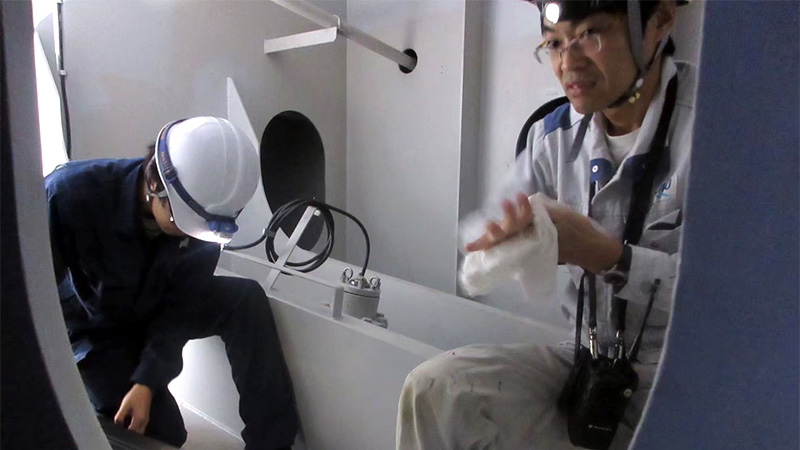
During the measurement work (left: Mr. Igarashi)
Measurement of the Stern Flow Field
Using a doppler sonar from Furuno, we measured the velocity of water current around the stern (the stern flow field). The doppler sonar we used this time, called a multi-layer current meter, was developed in the joint research of NYK, MTI, and Furuno, and can grasp the current velocity distribution of ship bottoms.
For enhancing the propulsion of propellers, it is important to understand what kinds of flow fields propellers are moving in. At the designing point we use CFD, but we can use the measured results to confirm if the CFD is correct or not.
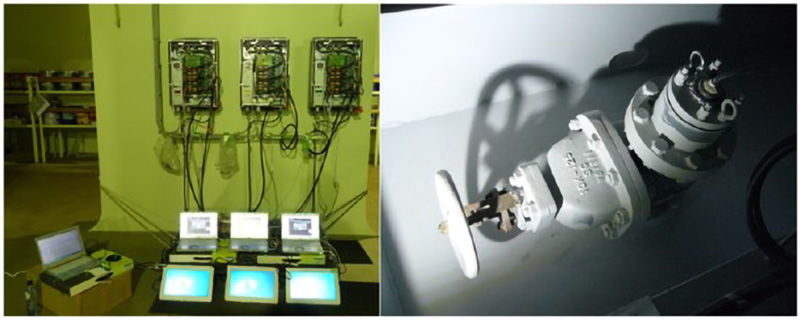
Measuring equipment for stern flow field (left: control panel, right: doppler sonar)
Observation of Cavitation
Cavitation is a phenomenon in which vapor pockets (bubbles or partial vacuums) rapidly form and collapse near the surface of propellers as they rotate underwater. If there are too many pockets, the propulsion efficiency may decrease, and propellers may be damaged. Therefore, at the design phase we design and built propellers after estimating, using the results of towing tank tests, how cavitation will be generated. Until now, we could not confirm if we could thoroughly replicate the actual ship condition in towing tank tests, but by comparing the cavitation we observed this time with the results of towing tank tests, we can now confirm the accuracy of the towing tank tests.
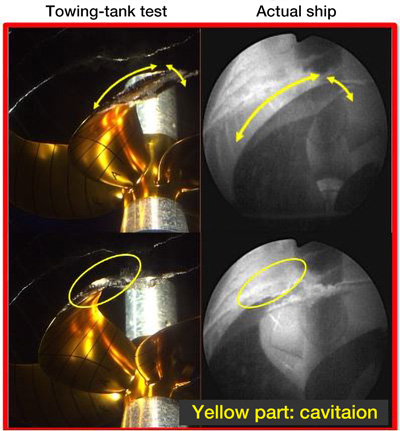
Measurement of Fluctuating Pressure of Stern
Along with fluctuating cavitation, generated by propeller rotation underwater, pressure fluctuation occurs in the water, which transmits the fluctuating pressure to the hull, where the water pressure on the stern’s planking also fluctuates. Since this pressure change also causes the hull to shake, it is estimated at the design phase so that excessive fluctuation pressure does not occur. This time, a pressure sensor was used to measure changes in water pressure acting on the stern planking. By comparing the result with the estimation at the design phase, it is possible to confirm the estimation accuracy and the error factor.
During this boarding, the measurements went smoothly. I appreciate the crew members’ great cooperation with our work. NYK and MTI secured valuable measurement data on propellers and more, JMU compared and analyzed the data with design values, and Furuno adjusted the measurement programs and confirmed data quality. Each company utilized its own specialized field, and as a result we were able to collect such interesting and useful data. This measurement might not have been achieved without the cooperation of all three critical entities: a shipping company, shipyard, and measuring-device manufacturer.
Utilization of the Data
By utilizing a part of the data collected through this measurement, we successfully improved propeller performance on a same-type ship (sister ship) by 1.2 percent. From now, if the detailed analysis of the measured data progresses, the accuracy verification of actual ship scale CFD will also progress. In the future, we plan to carry out measurements on various ship types other than containerships. Thus, I think, if we can build a cooperative structure with each company, collect data in actual sea, and utilize high-precision actual ship CFDs for designing hulls and propellers, it will lead to the realization of higher-performance ships.
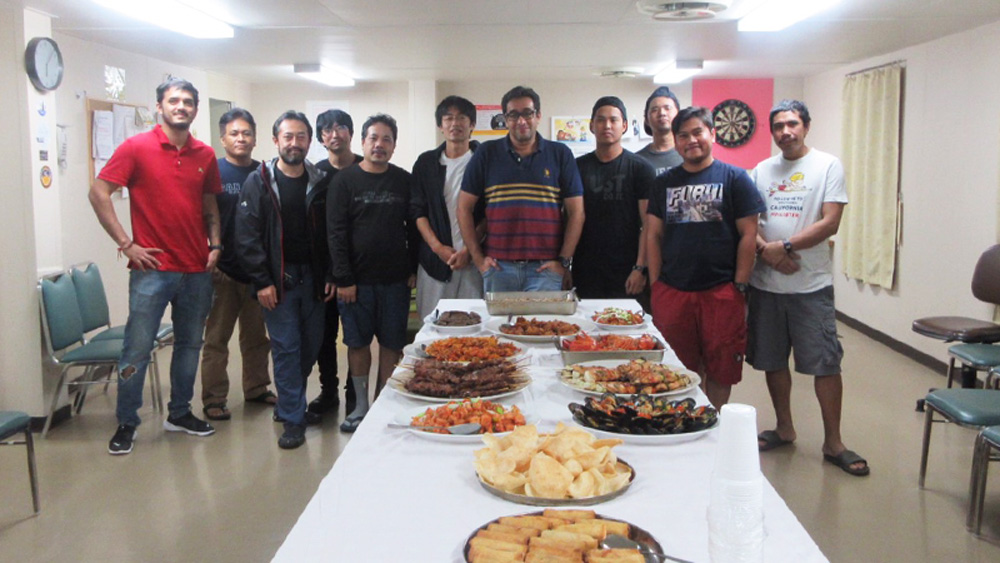
With crew members (Fourth from the left is Mr. Igarashi)
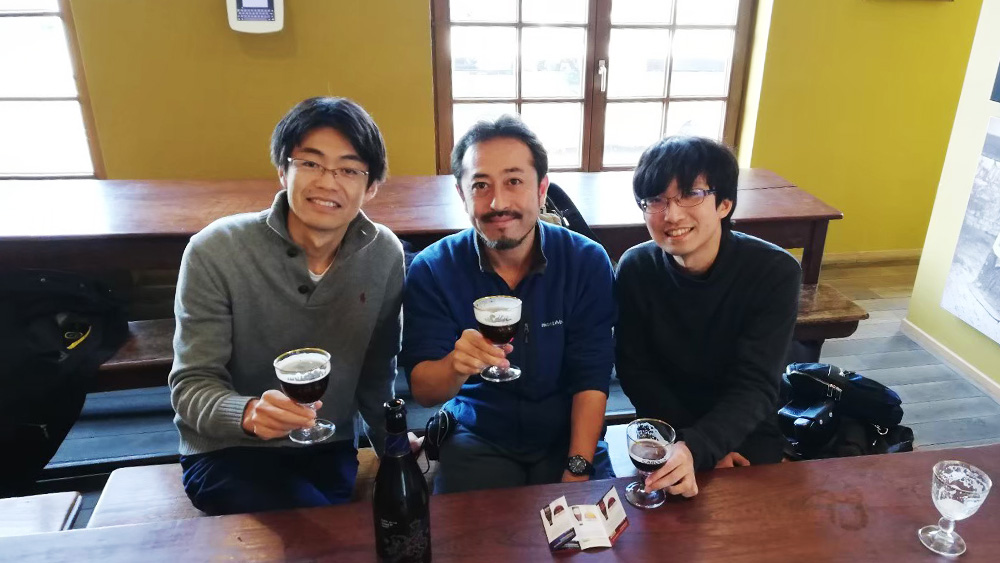
A short break in Antwerp, (Mr. Igarashi in on the right)