MTI Journal
MTI Journal.04
Development Story
for and by a Marine Engineer
Yohei Ide
Principal Researcher, Maritime Technology Group*
*The job title is as of the publication date
Safe vessel operation comes first
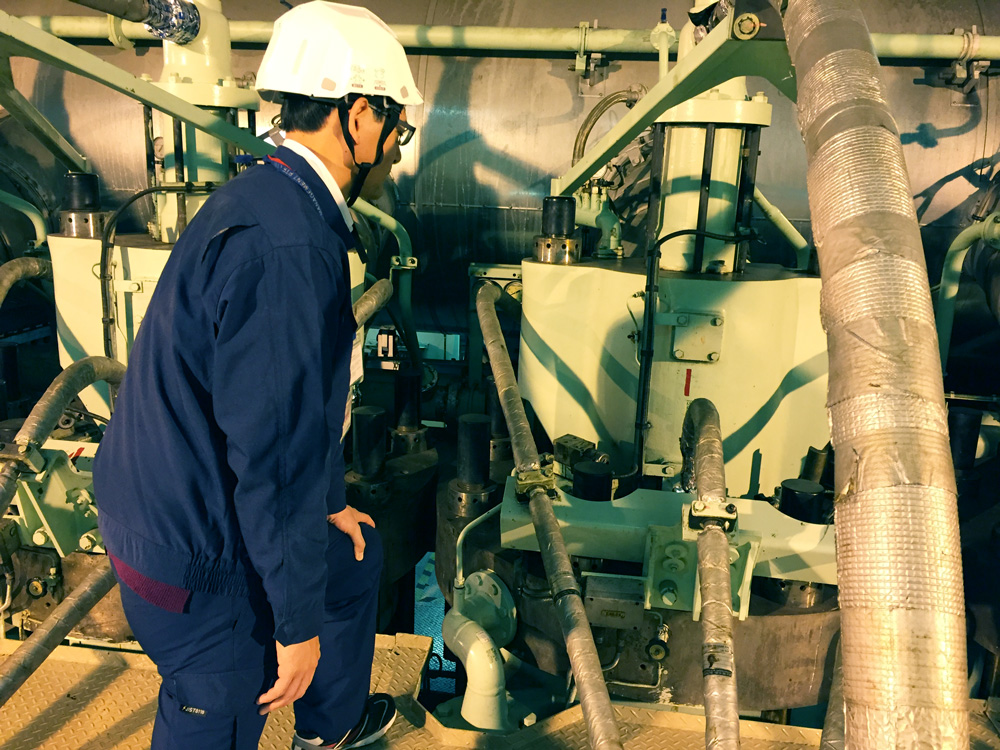
I first worked on land in 2012 and was in charge of bulkers’ fuel-saving activities. After that, I experienced two voyages on LNG ships, and in 2016, my life as a researcher at MTI started.
For improving prognostics and health management (PHM) for vessel machinery
At MTI, we focus on R&D projects for improving prognostics and health management (PHM) for vessel machinery as one of the activities for safe ship operation, and aim for realizing condition-based maintenance (CBM) not based on operating time as before but based on the conditions of machinery. Successfully realizing CBM demands that users (crew members) collaborate with ship-machinery manufacturers that have ship-designing know-how. The collaborative sharing of actual operation data or information and exchanging of feedback with one another can improve machinery performance. Realizing CBM not only prevents accidents by detecting anomalies but can also streamline the system integration (advanced network), which means that we can better than ever grasp the conditions of all individual instruments and integrate them with a system. In the following chapters, I will introduce Kirari NINJA and UMS check system, which were developed for realizing CBM.
Can we inspect the interior of a vessel engine more easily and precisely?
There are two ways for inspecting a vessel engine’s combustion chamber. One is called overhaul inspection: a crew enters the inside of the engine after having stopped the engine. Because it is dark inside, it is hard to see in detail, so the crew is required to work long and hard there in high temperatures. The other one is an inspection by looking in or taking photos of the interior from the scavenging port. This inspection is easy but cannot see the top area well, and injury might result if an inspector were caught in the piston; there are some disadvantages.
But given the convenience of non-opening inspections, my predecessor, also a marine engineer, was always thinking about it and asking herself if she couldn’t somehow inspect the inside of the combustion chamber safely without opening the engine . . . and fortuitously found a 360-degree panoramic camera on TV and got a bright idea. Soon after that, I developed a prototype device and tried taking some photos on a vessel, whereby various issues emerged: we needed some refrigerants because the temperatures inside engines became higher than one might imagine, or the sizes of scavenging ports varied depending on vessels, and such. Yet we overcame these issues and, through extensive trial and error, finally completed Kirari NINJA. By installing it on the upper part of the piston in the combustion chamber, photographs in all directions of the interior can be taken during one round of vertical piston movement (in about 10 minutes).
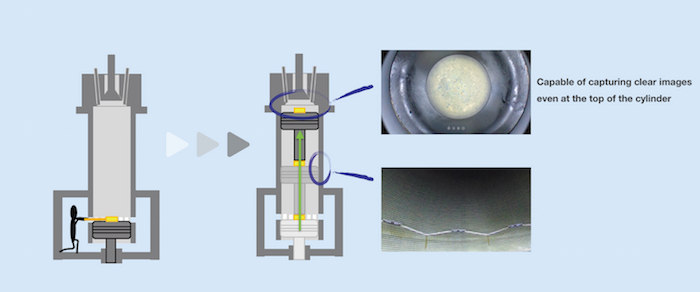
Non-opening inspection utilizing Kirari NINJA
Kirari NINJA makes it possible to grasp the conditions of the interior of the cylinder liner “by anyone, easily, safely, frequently.” Captured images can be compared with past images and the operational data; thus; it is possible to figure out how the engine operated in the past, which leads to an early detection of the causes of incidents and defects, and, consequently, prevents machinery accidents and optimizes the maintenance frequency – all of which promises to reduce life-cycle costs.
Digitization of large numbers of checks
Let me introduce another development story involving a marine engineer. On a vessel, marine engineers conduct a UMS (unmanned machinery space) check every day. Before an engine plant and equipment are operated unattended (e.g., at night), measurements must be taken, and taking such measurements is called a UMS check. In a conventional UMS check, the person in charge monitors equipment by conducting nearly 1,000 to 2,000 checks, manually recording the collected data on paper that, in a week, amounts to about fifty A4 sheets. Moreover, it is difficult to notice the changes in values with the paper-based check. If engineers want to refer to past information, they must search for the necessary information from amid the many sheets of paper. And if any trouble occurs, they first need to copy the data from paper to Excel for sharing numerical data with onshore staff, which consumes a lot of time. At MTI, from the thought of an engineer – “Can we make it much easier?” – we developed an electronic UMS checklist and its operational system. Further, these electronic checklists can be input with mobile devices.
When we started the development, we had a lot of responses from vessels and received various feedback. We struggled with many requests, such as “Can you change the button location?” from detailed ones to technically challenging ones, but the experience was thoroughly worthwhile. In addition, as one of the issues, the name of each instrument varies slightly depending on vessels. Even the same kind of instruments are recognized as different ones, and the graphs are created differently, so it is difficult to merge each vessel’s data and create graphs covering all vessels. We linked the slightly different names one by one in three months with the help of other engineers. But, just as we were about to finish up the software and disseminate it to vessels, the security policy was changed and we had to start over again and create the software from the first.
By digitizing data, it’s possible to get necessary information promptly; that plus the visualization with graphs lead to an early detection of anomalies. If any anomaly is found, we can save data together with photos or videos taken by tablets and thus share the condition much easier than before. In addition, we can send data through this system, so we can support vessels from the shore side because it’s possible to grasp the auxiliary data that cannot be extracted with SIMS (Ship Information Management System.)
In the future, we hope to develop a function to report anomalies detected by the system. That notification is to be simple and easy. Moreover, this system has a possibility to be applied for other checklists, not only for the UMS check, so we continue developing to realize it.
Hopes in the improvement of prognostics in the future
As an engineer, I feel that improved prognostics will mean realizing a far earlier detection of anomalies. And as a crew member, I appreciate how early detection and the ability to cope with troubles from an early stage will bring everyone an enhanced sense of reliability. When I return to working aboard, one of the products that I helped to develop should be on board as well. I look forward to actually using it, as I can review the product from the other aspect.
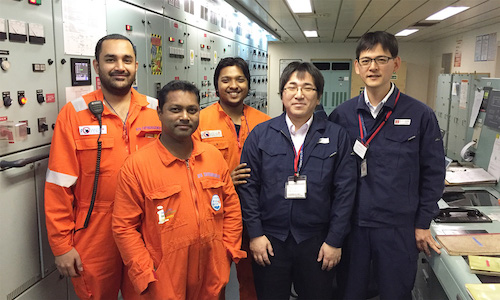
Visiting a ship for on-board system maintenance