MTI Journal
MTI Journal.20
Condition Based Maintenance (CBM) in Ship’s Main Engines
Tsuyoshi Tera
Principal Researcher, Maritime and Logistics Technology Group*
*The job title is as of February 28, 2023
I was seconded to MTI in April 2021 from ClassNK, and now being engaged in R&D for realizing Condition Based Maintenance (CBM*1) for marine equipment, mainly for main engines. I would like to contribute to the safety and efficiency of ships from the perspective of what CBM methods can be used to solve current issues.
Current Issues
Time Based Maintenance*2, or TBM, which is currently used in ship maintenance guidelines, requires periodic inspection and maintenance of each equipment regardless of its condition. While the TBM method of inspection and maintenance has the advantage of making the timing of maintenance more predictable, if the maintenance intervals are improperly set or if the maintenance execution at the set intervals is not followed, there is a risk of serious damage or, in some cases, uneconomical operation. NYK and MTI respond to these issues by performing maintenance according to the condition of each equipment, rather than at preset intervals. We conduct R&D on inspection and maintenance methods based on CBM, a method of diagnosing equipment soundness through data monitoring and analysis and performing maintenance at an appropriate time, and some of our research is conducted in collaboration with classification societies and engine manufacturers.
The NYK Group has Ship Information Management System*3 (SIMS), which is a system for timely sharing of hourly detailed data on vessel operations, fuel consumption, equipment status, etc., between vessels and shore, and there is a foundation for analyzing various data, including vessel operational data. Thus, we have been studying condition monitoring of ship equipment that also utilizes data from SIMS.
Establishment of a System of Condition Monitoring Equipment
If crew members could monitor the condition of equipment and measured data 24/7, it would be possible to detect anomalies before major accidents occur, but it is not realistic to constantly monitor the condition of various equipment on operating ships for detecting anomalies that do not occur frequently. Until now, maintenance and condition monitoring of each equipment was conducted by crew members. However, with the recent trend of IoT (Internet of Things), digitalization of business is progressing, and communication utilizing communication technology (ICT: Information and Communication Technology) is also becoming popular.
At NYK/MTI, by introducing LiVE*4(Latest Information for Vessel Efficiency), now we can monitor the engine conditions to some extent even from shore, and we can deal with various issues by sharing information between ships and shore.
In view of these circumstances, NYK and MTI are conducting a joint research project with an engine manufacturer and a classification society, starting in November 2019, as follows, with the aim of realizing condition monitoring of main engines.
Project | Partners |
Joint research for realizing CBM for main diesel engines | NYK, MTI ClassNK Japan Engine Corporation |
CBM in the Joint Research
In promoting this joint research, we first considered the need for CBM in this research as follows.
While ship classes, manufacturers, and shipping companies have different requirements for marine equipment, the requirement of “preventing engine accidents” is considered to be common. In addition, in the present TBM, open-up inspection is to be performed when the time comes, regardless of the condition of the equipment, which means that the equipment is to be maintained at a time even if it is still usable. Conversely, in some circumstances, the limit may be reached before this maintenance interval is come.
We thought that if we could constantly monitor the condition of the equipment, then we could eliminate these problems, optimize inspection and maintenance standards, and prevent serious engine accidents. Constant monitoring of the condition of the equipment is to be considered as CBM.
This research is a joint research project by a classification society, manufacturer, and shipping company, and we believe that the three organizations have worked together to develop methods to optimize inspection and maintenance standards and to improve the certainty of preventing engine accidents.
In addition, by implementing CBM, as a shipping company, it will be possible to increase the availability of individual equipment by extending maintenance intervals and reducing downtime due to trouble, and also to prevent serious accidents by identifying signs of equipment damage. As a manufacturer, it is expected to contribute to improved product reliability and to create new after-sales services by constantly monitoring the status of the product, which is expected to add value compared to conventional equipment. As a classification society, there is a possibility to improve of inspection quality. Although the goals of each organization are different, we have conducted this research because we believe that the realization of CBM will be beneficial to the three organizations involved in this joint research. The relationship between the three organizations in this joint research is conceptually depicted in the following diagram.
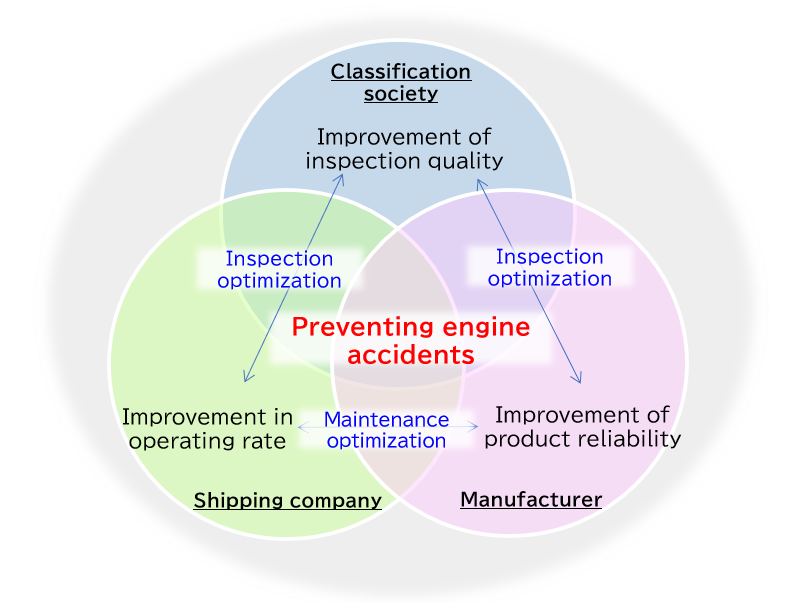
Relationship between the three organizations in the joint research
Toward the Selection of Condition Monitoring Equipment and the Realization of CBM
We have decided to implement the study by establishing the above-mentioned structure. On the other hand, in each marine equipment, it is unclear “what” and “how” to monitor the status of the equipment. Unless these are clarified, it is difficult to say that the condition of the equipment is being monitored, so first, we conducted a study with our joint research partners to determine which components of which devices should be monitored for their condition.
This time, we decided to examine the condition monitoring of marine main engine, and we grasped “how” failures of the marine engine plant “occur” in “which part”, “what impact” they have, and “how” they are currently “prevented”, “evaluated” their “effectiveness”, examined methods to “replace” the evaluated methods with “data monitoring”, and further “confirmed” their effectiveness. Utilizing such a study flow, we examined the feasibility of CBM with the goal of being able to implement CBM in a manner that does not increase risk compared to conventional TBM.
Actual selection was made utilizing the risk assessment methodology as described in ClassNK’s CBM Guidelines, 2nd Edition*5. First, a functional decomposition tree (FDT) is conducted to decompose each component of the main engine according to its function. Then, utilizing the HAZID method, failure modes are identified for each function, and a Fault Tree Analysis (FTA) is created to analyze the cause of the failure for the effects of each identified failure mode. Finally, for each node of the FTA, parameters are derived to determine its status.
We then used a risk matrix to evaluate whether CBM could be implemented with the monitoring parameters derived from this study methodology. Consequently, since CBM was recognized as feasible, an event tree (ETA: Event Tree Analysis) was drawn to analyze actual events that could occur in order to derive each threshold value, and a range of acceptable, avoidable, and unacceptable phenomena was defined.
The monitoring method developed in this way was eventually subjected to a risk assessment that introduced cost-effectiveness and was judged to be feasible in terms of cost, so the method developed in this methodology is to be used for CBM implementation.
In practice, the main bearing of a large marine diesel engine is used as the monitoring part, and the main engine’s main bearing lubricating oil outlet temperature (LO outlet temperature) is selected as the monitoring parameter. In order to confirm the validity of this monitoring parameter, LO outlet temperature, we conducted a land-based test simulating the operating conditions of the actual machine and confirmed that it correlates with each change in the actual machine and also reflects the condition of the main engine’s main bearing as a monitoring parameter.
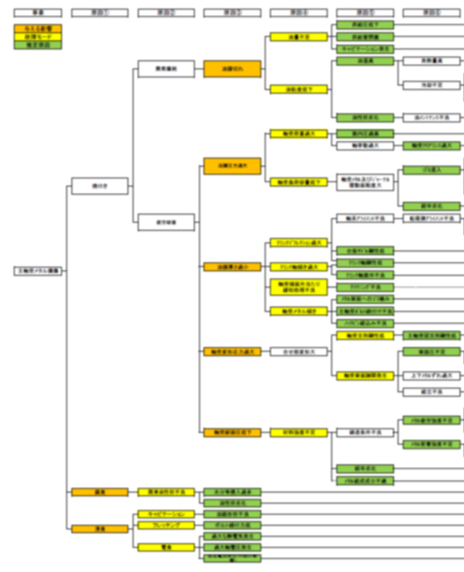
Example of FTA
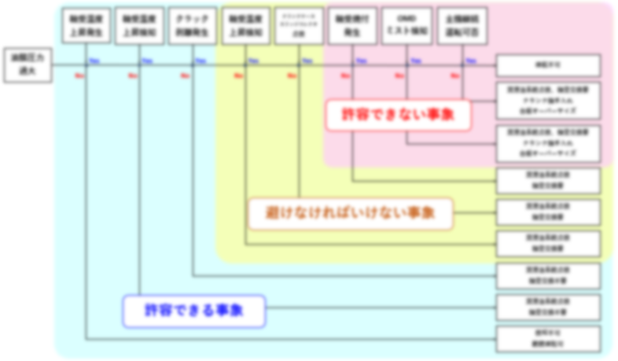
Example of ETA
Application to the Operating Ship
As mentioned above, we decided to measure the LO outlet temperature to monitor the condition of the main engine’s main bearings. In order to apply this method to an operating ship, we installed sensors in the main engine of the NYK Group-owned coal carrier Noshiro Maru with the cooperation of the main engine manufacturer.
A temperature sensor has been installed on the saddle of the Noshiro Maru’s main engine plate to measure the LO outlet temperature of the main bearings of the main engine. The data acquired from the temperature sensor is combined with the vessel’s operation data obtained from SIMS through an application on board the vessel, and the combined operation data and temperature data are sent to shore in real time via ship-to-shore communication.
The data sent to shore are stored in a database on shore, which is visualized and monitored by classification societies, engine manufacturers, and shipping companies.
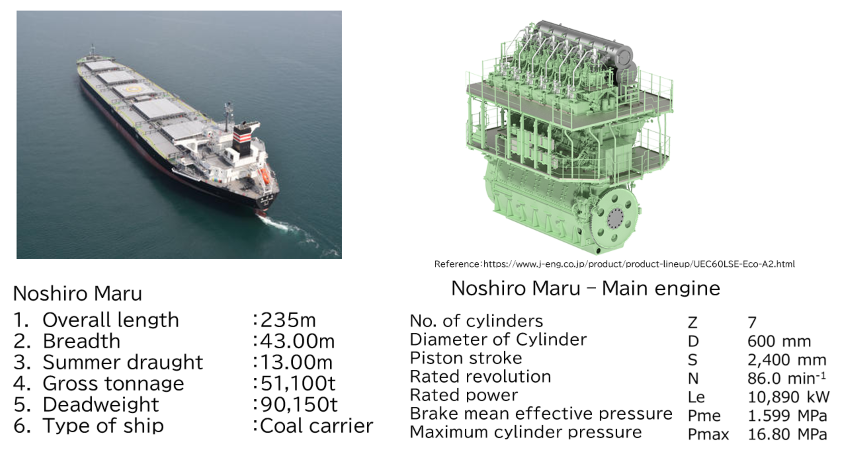
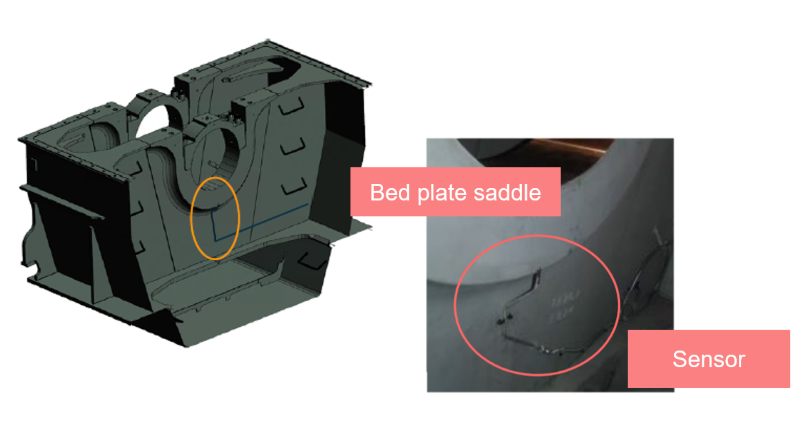
Overview of LO outlet temperature sensor installation
Development of Monitoring Tool for Acquired Data
MTI has developed the “Diesel Engine Main Bearing Condition Monitor (CBM Viewer)” as a tool for monitoring LO outlet temperature and other data obtained from the vessel.
This viewer links LO outlet temperatures acquired from sensors installed in the main bearing of main engine with ship operation data acquired from SIMS and displays them in real time, allowing data to be shared with ship classes and engine manufacturers. From those acquired data, the system has the ability to determine whether or not damage has occurred in the main bearing of main engine due to changes in LO outlet temperature, and to display the status of the damage like a traffic light. Data is shared in real time between the shipping company, engine manufacturer, and class, so that appropriate action can be taken in response to the detected damage.
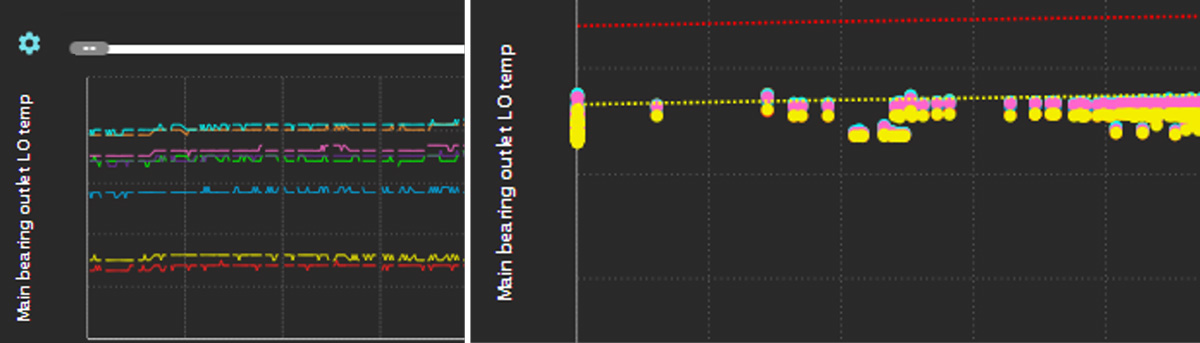
Diesel Engine Main Bearing Condition Monitor – Example of sensor data graph
Received Approval from ClassNK for CBM Inspection Method
Through these efforts, the CBM for the main bearing of main engine applied to Noshiro Maru was approved by ClassNK in September 2022 for the CBM maintenance method, and the main bearings of main engine was changed from the conventional TBM method to the CBM method.
Future Outlook
Although various studies for the realization of CBM, such as installation on board, adaptation, inspection, and approval, may be a small step from the perspective of marine equipment as a whole, we believe that we have achieved a CBM method which has solid technical background. We hope that this series of studies will help the maritime industry to consider CBM.
In the future, we would like to increase the number of applications to main bearings of main engine and further refine the monitoring method we have developed this time, and we will continue to study other equipment and explore feasible CBM from time to time.
If we can realize an “autonomous CBM” in which AI (artificial intelligence) judges the condition of the vessel and also determines the timing of equipment maintenance, we expect it to be useful in reducing the recent shortage of seafarers and work in hazardous locations. We believe that even if these technologies are not established immediately, further studies will contribute to the reduction of serious engine accidents, the creation of new technologies for efficient and safe ship operation, and the further development of existing technologies in the future.
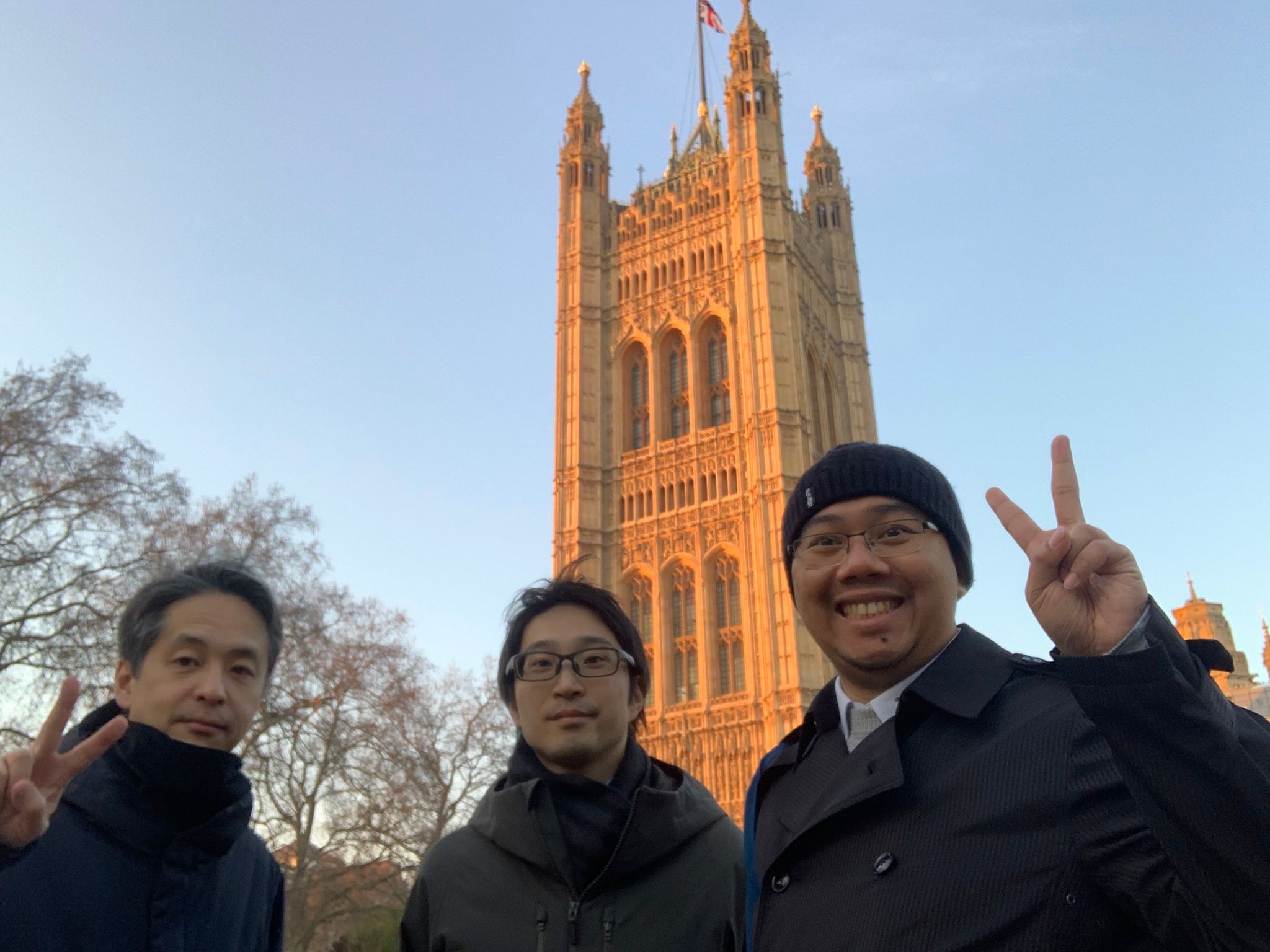
In London on a business trip (center is Mr. Tera)
*1 Condition-based maintenance (CBM):
A maintenance strategy that monitors the actual condition of an asset to determine what and when maintenance needs to be performed, rather than awaiting machinery failure or conducting maintenance on a regular basis
*2 Time-based maintenance (TBM):
A maintenance strategy in which replacement cycles are predetermined for equipment and parts that fail periodically
*3 SIMS (Ship Information Management System):
A system developed by the NYK Group for the timely sharing of detailed hourly vessel data, including operational status, fuel consumption, and equipment condition, between ships and shore.
*4 LiVE (Latest Information for Vessel Efficiency):
The application displays the operating ship’s position, speed, fuel consumption, etc. on the screen based on data sent from the ship, allowing the operator to monitor the ship’s fuel consumption and other information to support optimal operation
*5 CBM Guidelines (Edition 2.0):
Case studies based on risk evaluations of CBM implementation. Published by ClassNK.