Pursuing overall optimization through Operation × Hardware
August 29, 2018
■Enhancing the preventive maintenance of engines from the user’s point of view
Nippon Yusen Kaisha (NYK) and Monohakobi Technology Institute (MTI) are currently working to enhance the quality of preventive maintenance of engines with the help of actual operation/navigation data in a bid to realize improved safety and efficiency in ship operation.
The first step was “visualization” through the user’s point of view. Some of the representative tools that they use toward that end are: (1) the “LiVE for Shipmanager” and “LiVE for Chief Engineer” that extract sensor data collected through such systems as SIMS (Ship Information Management System), which is deemed important or necessary from the user’s point of view, and then process the data into graphs so that the data looks a lot more interesting; (2) the “electronic-check system,” which allows data to be directly input into a tablet, enables the collection of data about auxiliary machines and other equipment that have no sensors for transmitting automatically as a signal; and (3) the “Kirari NINJA” that makes it possible to have a visual of the state inside the engine’s combustion chambers without dismantling the main engine. These tools make it easier to share information between ships and onshore facilities, leading to the provision of better support from land.
What they are working on next is “notification based on preset rules.” For instance, the alarm functions of “LiVE for Shipmanager” and “LiVE for Chief Engineer” will be used to send out a warning or alarm containing know-how on the occurrence mechanism of troubles or failures likely to occur in actual operation. The “abnormality detection alarm” now under development will be designed in such a way that it will be able to grasp accident risks at an earlier stage without being affected by the individual experiences of those involved by transforming the knowledge of trained chief engineers into logical data.
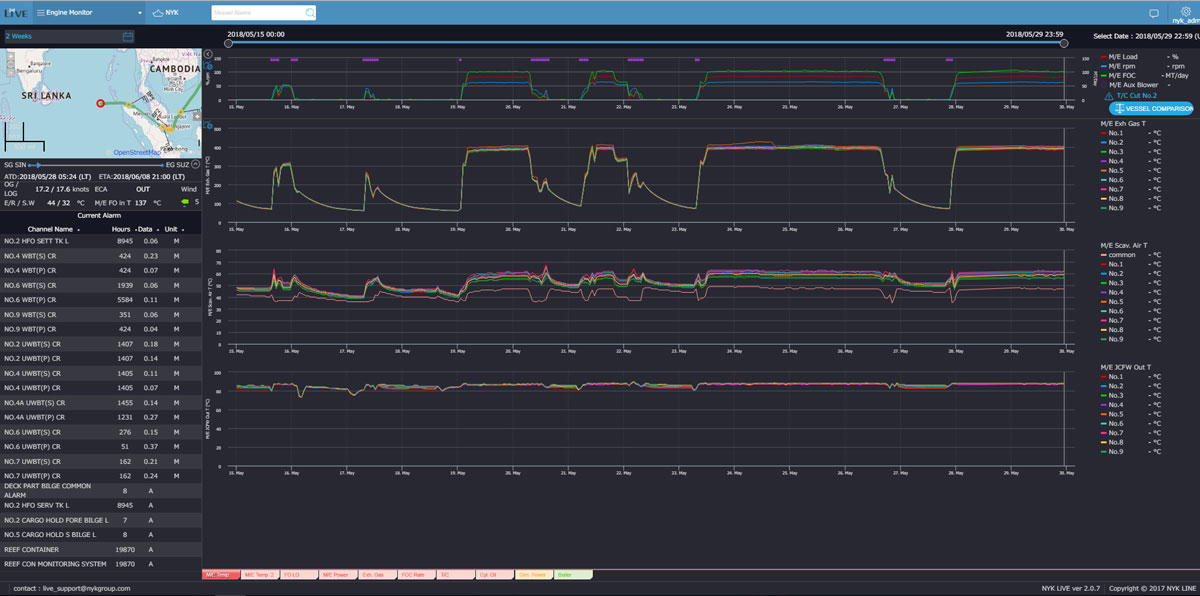
Screen image of “Live for Chief Engineer”
■Pushing toward maintenance based on condition
NYK aims for collaboration with various companies whose design know-how can help in advancing the creation of a preventive-maintenance system that can also enhance accuracy in “notification based on preset rules” and promote the establishment of a new preventive-maintenance method in the future. They believe that adding design know-how into the process will enable a more accurate diagnosis of the current condition.
NYK and MTI are not aiming to build a conventional maintenance system that sets maintenance intervals after certain amounts of time or use, but a rational maintenance system that is based on the actual condition (condition-based maintenance, or CBM). For instance, it is important to know the amount of wear on a cylinder liner, but in order to check the actual condition, it is necessary to dismantle the main engine, which is very time-consuming. But by making it possible to check inside the engine and analyze the amount of wear through photos without opening the engine, assessments of the state inside the engine can be done more frequently and open-engine maintenance can be done at ideal scheduled times. As a user dealing with entire engine plants, NYK is considering implementing CBM not only for main engines but also for various marine auxiliaries.
The initiatives toward realizing CBM cannot be advanced by a single company on its own. These initiatives are fueled by collaboration with marine equipment manufacturers, shipyards, and other relevant sectors. The final goal is to create a new product/service that has never been seen before by bringing together the operation know-how and on-site actual data of NYK as a user and the design/manufacturing know-how of manufacturers.
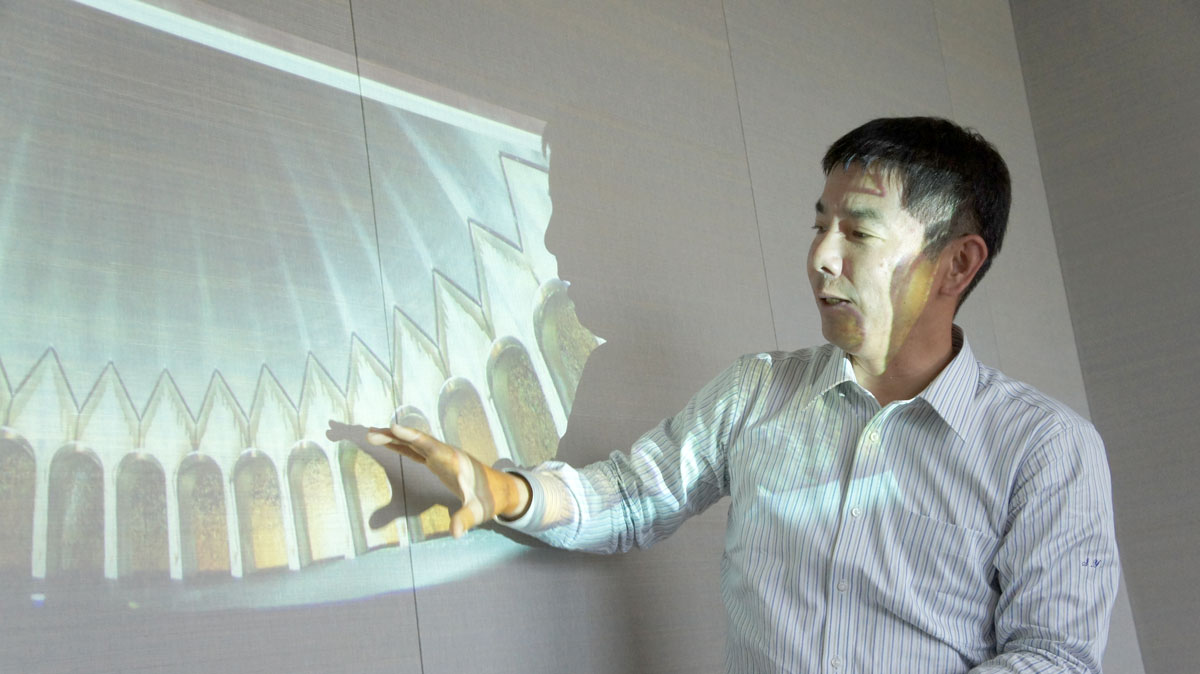
Image of the inside of the combustion chamber shot by “Kirari NINJA”
■Other examples of initiatives
Project/Partner Company | Details | Significance for NYK and Partners, and Future Developments |
Hull structure health monitoring
Nippon Kaiji Kyokai (Class NK)
Japan Marine United (JMU)
National Maritime Research Institute
Japan Weather Association
Yokohama National University |
A hull structure health monitoring system that can measure stress applied to the hull structure is a standard feature on ten 14,000-TEU containerships. By obtaining and analyzing the stress values together with navigation data in actual seas, partners will develop a method for estimating the stress-and-fatigue life of the entire ship structure in actual seas, and a system that can support navigational safety. | At the ship-design stage, the force (stress) applied to the hull under various atmospheric/hydrographic conditions is estimated to ensure the required hull strength and structure. The large-scale collection and analysis of the forces to which the hull is subjected in actual seas and the provision of feedback on the results to the marine engineering division will contribute to the construction of better-performing ships. By developing a method for estimating the stress-and-fatigue life on areas other than those measured, enabling the prioritized checking of areas predicted to be prone to strength reduction during dry-docking and the provision of ship-strength data when sailing ships, the asset value of ships will also be maintained or enhanced. Further, it will be possible to support better navigational safety if the condition of a ship’s hull can be relayed to the ship’s officers during navigation. |
Remote condition monitoring and diagnostic system of marine pumps
Naniwa Pump Mfg.
Eagle Industry |
NYK has reproduced the anomalies of marine pumps, such as impeller damage that can occur on board, at the Naniwa Pump testing site onshore to acquire and then review fault data. To accomplish this, pressure sensors and vibration sensors were attached to pumps in operation on the ship in order to capture actual operation data. Researchers are using this data to develop a condition-monitoring system for the pumps so they can realize advanced navigational safety and remote monitoring through data communication between sea and shore by shifting to condition-based maintenance (CBM) from time-based maintenance in the prediction of pump anomalies in the future. | For users that must observe functions and think of efficiency enhancements for the entire plant, the maintenance of auxiliary machines likes pumps is important work. Equipment, regardless of size, must be inspected for a shift to CBM, and every effort is being made to ensure the understanding of manufacturers. In 2016, they conducted a trial on a bulker by installing a pump condition monitoring system that they had developed, and they have been collecting data ever since. This system can also be used to predict failures in other equipment in the future. On the significance of collaboration with NYK, Naniwa Pump said, “By incorporating the views of actual users, we are able to directly reflect the information and functions that they want into our products. Further, the data on products that are installed in ships and plants, which is difficult for manufacturers to get their hands on, proved helpful in the development of products.” Eagle Industry stressed, “We see it as an extremely helpful project for selling products that are useful to society at a reasonable price. We were able to hear the voices of customers, something that is normally hard for parts manufacturers to get, and we hope to reflect those into the development of next-generation products.” |
Kirari NINJA Dashboard | The Dashboard enables them to compare a series of images shot over time by Kirari NINJA, which automatically takes 360-degree photos of the insides of a cylinder and is installed on an engine’s piston when the ship is at anchor in harbor. The Dashboard allows them to visually confirm the changes in condition inside cylinders. The system also incorporates a function for displaying the operation data obtained through SIMS and the images side by side. This system has already begun trial operation. | With the Dashboard, NYK is able to confirm the changes in condition inside the cylinder along the time axis, estimate the cause of the changes in condition, and then determine the appropriate amount of lubricating oil. They will advance the miniaturization and reduction of power of the Kirari NINJA so that it can be used on engines with small-diameter cylinders. |
Cylinder pressure sensor |
NYK has built a system that can acquire data from a ship equipped with combustion chamber pressure sensor that can constantly monitor the pressure inside the cylinder in order to directly capture the combustion condition of the engine and other elements, and then send that data onshore via SIMS so that it can be verified by the onshore viewer. This system has been used since April 2018. | The even use of multiple cylinders is ideal, but if one cylinder is running at a different combustion pressure, it means that the engine is not attaining its optimum performance. The pressure sensors are used for comparing the cylinder pressures of multiple cylinders, identifying the cylinder with deviated pressure, and then assuming the cause of deviation. They are now advancing a project that gathers such data and uses them to prevent accidents in ships where measurement is done manually, and not through constant monitoring. |
Next-generation operation support system “J-Marine NeCST”
Japan Radio Co., Ltd. (JRC) |
NYK has developed a tool that enables the creation of nautical plans on a large easy-to-use touch-panel display, supports onboard work and operations, and possesses a communication function for sharing information between ship and onshore facility or between vessels through the Cloud. It will also be introduced in the crisis management office at NYK headquarters. Through coordination with the J-Marine NeCST that will be installed in ships and onshore facilities, the operation data can be more quickly obtained by the onshore office, resulting in more expeditious crisis response and a safety management system with a higher quality. | Given the mandatory installation of ECDIS (Electronic Chart Display and Information System) on ships, they have developed a system that incorporates the needs of captains and mates who seek the convenience of paper sea charts. Aside from being installed on the cruise ship Asuka II, it is also scheduled to be mounted on a newbuilding that will be commissioned in fiscal 2018. |
Simulating inside condition of cylinder liner
Diesel United (DU) |
Depending on environmental factors such as humidity and the engine’s operating condition, condensation forms inside the cylinder, causing sulfur in the fuel oil to change to sulfuric acid, which leads to low-temperature corrosion. They are currently developing a system to gather and compute data in real time on the corrosion risk distribution on the cylinder surface to eventually control the risk of abrasion and other corrosion-related damage inside cylinders. In the future, they will verify if the parameters and calculations set in the system are correct by installing the system on 14,000 TEU containerships. | Although the risk of low-temperature corrosion depends on the external environment, managing that risk is not currently performed by controlling the amount of injected engine and cylinder oil. They are targeting the realization of real-time automatic control of cylinder oil injection amount based on the environmental conditions in the engine room. Further, for future CBM they aim to accurately capture the current condition as the first step in grasping the remaining life. Diesel United commented, “The manufacturer can take charge of everything up to simulation, but collaboration with users will ultimately be necessary in finding out how it will be used and what benefits can be reaped from it. Our collaboration with NYK, which is proactively engaged in this area, is more interesting than anything else.” |
Advanced alarm using water-in-oil sensor |
NYK used to send lubricating oil extracted in regular samplings to an onshore analysis institution to be evaluated for absolute moisture content in order to discover whether the oil had been mixed with water, which is one of the main causes of damage to bearings. In recent years, an alarm system that enables real-time onboard monitoring of the lubricating oil’s relative moisture content (how much has been mixed in the oil compared to the saturated moisture content) through sensors has debuted on the market, but in that system an alarm goes off if the relative moisture content exceeds the threshold regardless of the surrounding environment. To address this issue, they have developed an advanced alarm (patent pending) in which the threshold that will cause the alarm to go off changes according to the surrounding environment, i.e., according to the temperature and humidity in the engine room. It is possible to avoid one of the causes of bearing damage early. | NYK installed the sensor on a trial ship to measure the moisture content in the main engine’s lubricating oil and gathered data for more than a year. The results showed a strong correlation between the humidity/temperature inside the engine room and the relative moisture content. They also acquired know-how on sensor installation as well as ensured safety, so they are currently conducting another trial using a generator that has a higher bearing-damage risk than the main engine. By building an advanced alarm technology, they can grasp the penetration of water into lubricating oil on a real-time basis both aboard and ashore, leading to the detection of signs, preventive maintenance, and early detection of such anomalies. Further, the detection of moisture from sources other than the air will make it possible to find anomalies early in other related equipment and devices. As one of the activities for realizing CBM, it is expected that using this advanced alarm system might extend the interval between bearing overhauls or significantly reduce them. |
Condition monitoring and clogging prevention in fuel oil filters
Kanagawa Kiki Kogyo |
Multiple filters are installed on ships to remove impurities in fuel oil. These filters have an automatic or manual backwashing function to get rid of filter clogging, and the automatic backwashing is done regularly or when the pressure difference between the outlet and inlet has exceeded the threshold. NYK has installed a new type of control panel developed by Kanagawa Kiki Kogyo on two ships operated by NYK, and this panel gathers/transmits data about the condition of the filter. Using actual operation data on FO filters, Kanagawa Kiki Kogyo and NYK will study optimal backwashing methods to prevent clogging. | Clogging in filters is prevented through the automatic backwashing function and the overhaul cleaning done by crews around once a month. But filter cleaning is hard work, and severe clogging sometimes cannot be cleared by only washing. They thus aim to build a system that can validate and evaluate the parameters and other elements when effective backwashing occurs by constantly monitoring and analyzing various data such as the flow rate and the differential pressure between the inlet and outlet. External factors such as the properties of the fuel oil will also be considered, and they will strive to optimize the backwashing timing, interval, and the timing of the overhaul operation in order to keep the filters in sound condition. This was the first time for them to install this control panel on a ship on a full-fledged basis, and engage in communication and data-review for improvement. Kanagawa Kiki Kogyo commented, “We have long been handling filters, so we have heard a lot of talk about the qualitative aspects of the operation condition on ships. However, we have not yet encountered this massive raw data.” They pointed out, “By grasping the actual operation condition in a quantitative manner, we have learned a lot of things through this opportunity. These can be used when formulating proposals on the optimal operation method for filters and improving filters in the future. In that sense, it is an extremely meaningful project.” |
Remaining useful life of main engine’s combustion chamber parts
Japan Engine Corporation (J-ENG) |
The maintenance interval of the parts for the main engine’s combustion chamber is not set according to the actual usage condition such as the operation condition and combustion condition, with the fuel that is being used, but set based on operation time recommended by their manufacturers. By computing the engine load put on the combustion chamber parts from the past up to the present based on operation-related data such as engine rpm and load data, and the condition of the fuel being used, J-ENG and NYK aim to predict the remaining useful life of each part and build a system for performing maintenance according to the condition of each part. |
They are currently developing a system that will boost the precision of predicting the remaining useful life of parts by comparing the estimated remaining life based on data with the parts’ actual condition. This joint research with a main engine manufacturer serves as one of NYK’s initiatives toward the realization of CBM, and they expect that it will lead to the extension of intervals or elimination of overhaul inspections of the main engine’s combustion chamber. J-ENG commented, “By being on the same team as NYK, we have obtained opinions from the user’s perspective and big data in actual operation. We think these are essential toward the realization of CBM. While CBM will be a new business model, it does not necessarily mean only positive things for manufacturers, as we are aware of the issues we need to deal with and that the research details will be put to use in autonomous ships as well.” The company also discussed the meaning of its collaboration with NYK, saying, “By making the distance between our companies shorter, we are now able to approach each other easily. We are extremely grateful that opinions such as ‘we are actually running the engine in this way’ will now be heard right away. This is a win-win relationship that will lead to the improved reliability of engines for J-ENG and navigational safety for NYK.” |
Failure-detection system for water-level sensor to reduce incidence of dry-boiling in auxiliary boilers
Sunflame |
A shortage of water inside an auxiliary boiler that is used for heating fuel, cooking, and supplying hot water may lead to dry-boiling (heating without water inside), which could then necessitate replacement of the boiler. In light of this, NYK had installed a duplex safety interlock that would automatically stop the burner if water falls below a certain level. However, upon verification of data over the past 20 years, they found that more than half of dry-boiling incidents had been caused by a malfunction of this duplex water-level sensor. Sunflame and NYK have thus developed a function that will detect a malfunction of such sensors. | The principle may be simple, but NYK expects it to significantly prevent accidents. The burner manufacturer, Sunflame, integrated the function in a system installed on two containerships and two bulkers in 2017. They are eyeing it as a standard feature for ships operated by NYK. Sunflame explained, “We as a manufacturer were unable to find out why accidents were still happening despite the duplex safety interlocks.” Sunflame continued, “The manufacturer alone does not always know how the machines are being used by users. We might have thought that this matter would be difficult to resolve, but we were able to realize other options when we talked with NYK. Our company may be small in scale, but we were able to engage in open discussion to resolve NYK’s concern, even though it involved an unfavorable matter.” |
Contents
The NYK Group Tackles the Digitalization Challenge TOP
TOP INTERVIEW, Interview with Tadaaki Naito, President of NYK, – Striving to create new value
Infrastructures of the NYK Group in support of its aggressive stance with data utilization
Digitalization of ships – Challenge of technology development toward manned autonomous ships
Digitalization of navigation – Utilizing data in the field of dry-bulk shipping